DeCarbCH Wiki Technologies - Solar Energy
Solar Heat for Industrial Processes
Solar process heat is the utilisation of solar energy to provide heat for industrial processes that (ideally) require temperatures of up to 200 °C. This technology offers great potential as a renewable heat source for industrial applications, as it is sustainable and CO2-free and a predictable heat price ensures long-term planning security.
The choice of suitable collector technology depends mainly on the required process temperature. In addition to the collector technology, factors such as collector array size, storage volume and integration into the existing process also play an important role in the efficiency and cost-effectiveness of solar process heating systems.
There are different types of solar thermal collectors that can cover a wide range of temperatures, the most important of which are:
Flat-plate collectors (FPC) are effective for low- to medium-temperature applications and commonly used in residential solar water heating systems. They can also be employed in industrial settings for generating solar process heat, where moderate temperatures (up to around 100 °C) are sufficient. In solar process heat applications, they are often used to preheat water or air.
Evacuated tube collectors (ETC) and evacuated flat plate collectors (EFPC) are suitable for colder climates or at higher operating temperatures. They are used in the residential sector as well as for solar process heat, particularly in industrial applications where higher temperatures (up to around 120 °C to 150 °C) are needed.
Concentrating collectors, such as parabolic trough collectors (PTC) are particularly efficient at high temperatures and are therefore often used for industrial processes that require temperatures above 100 °C. They can reach temperatures of up to 400 °C and are typically used in regions with higher direct solar radiation. In Switzerland temperatures of 190 °C were reached in industry using this technology.
The integration of solar heat into industrial processes requires a holistic approach from the solar thermal system to the process and all other heat generation technologies in order to ensure efficient integration. The first step is to estimate the potential, for example by using a pinch analysis , which provides a valuable basis for the correct and optimised design and integration of solar heating systems. When selecting an integration point, the initial focus should be on processes with continuous energy demand in summer at the lowest possible process temperature not covered by heat recovery. It may be possible to reduce the process temperatures through process conversions, improved control, or efficiency measures. At the same time, it should be ensured that there is sufficient demand or storage capacity available at all times to fully utilise the potential. The more complex a process is, the more important are dynamic simulations. Dynamic simulation models not only enable the design of better integrated systems within processes, but also improve the understanding of the thermal-hydraulic and transient behaviour of solar thermal systems in connection with the requirements and constant changes in industrial processes.
Solar thermal process heat (SPH) generation is still a very small market with only a few installations registered. In the project EvaSP funded by the Swiss Federal office of Energy (SFOE) seven plants were identified and are being monitored, two of which have since been shut down
Choice of collector type
There are different types of solar thermal collectors that can cover a wide range of temperatures, the most important of which are:
Flat-plate collectors (FPC) are effective for low- to medium-temperature applications and commonly used in residential solar water heating systems. They can also be employed in industrial settings for generating solar process heat, where moderate temperatures (up to around 100 °C) are sufficient. In solar process heat applications, they are often used to preheat water or air.
Evacuated tube collectors (ETC) and evacuated flat plate collectors (EFPC) are suitable for colder climates or at higher operating temperatures. They are used in the residential sector as well as for solar process heat, particularly in industrial applications where higher temperatures (up to around 120 °C to 150 °C) are needed.
Concentrating collectors, such as parabolic trough collectors (PTC) are particularly efficient at high temperatures and are therefore often used for industrial processes that require temperatures above 100 °C. They can reach temperatures of up to 400 °C and are typically used in regions with higher direct solar radiation. In Switzerland temperatures of 190 °C were reached in industry using this technology.
Integration strategies
The integration of solar heat into industrial processes requires a holistic approach from the solar thermal system to the process and all other heat generation technologies in order to ensure efficient integration. The first step is to estimate the potential, for example by using a pinch analysis , which provides a valuable basis for the correct and optimised design and integration of solar heating systems. When selecting an integration point, the initial focus should be on processes with continuous energy demand in summer at the lowest possible process temperature not covered by heat recovery. It may be possible to reduce the process temperatures through process conversions, improved control, or efficiency measures. At the same time, it should be ensured that there is sufficient demand or storage capacity available at all times to fully utilise the potential. The more complex a process is, the more important are dynamic simulations. Dynamic simulation models not only enable the design of better integrated systems within processes, but also improve the understanding of the thermal-hydraulic and transient behaviour of solar thermal systems in connection with the requirements and constant changes in industrial processes.
SHIP in Switzerland
Solar thermal process heat (SPH) generation is still a very small market with only a few installations registered. In the project EvaSP funded by the Swiss Federal office of Energy (SFOE) seven plants were identified and are being monitored, two of which have since been shut down
Saigne -légier |
Fribourg | Bever | Yverdon | Langnau | Gränichen | HUG | |
---|---|---|---|---|---|---|---|
Status | Active | Active | Not Active | Not Active | Active | Active | Active |
Sector | Dairy | Dairy | Dairy | Roads | Dairy | Melting | Hostpial |
Usage | CIP, Prod. | CIP, Prod. | CIP, Prod. | Bitumen | CIP, Prod. | Varnish | Steril. Build. |
Temp. | 117 °C | 120-160 °C | 190 °C | 90-160 °C | 55-95 °C | 90-110 °C | 105-140 °C |
Collector | PTC | PTC | PTC | VFP | VFP | VTC | VTC |
Size | 627 m2 | 581 m2 | 115 m2 | 360 m2 | 240 m2 | 184 m2 | 512 m2 |
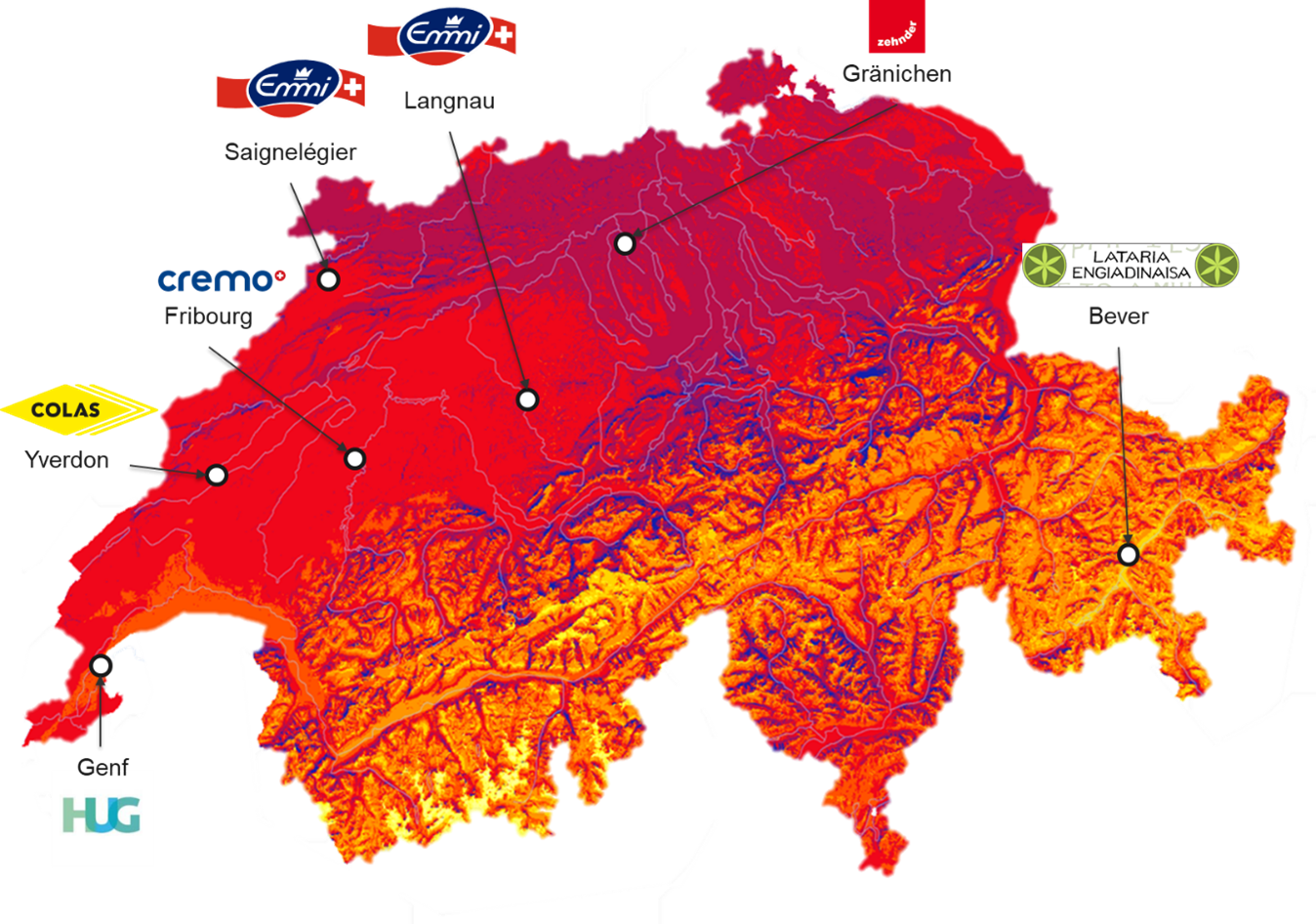
Energieschweiz has decided to promote the further spread of solar process heat in Switzerland by providing financial support for feasibility studies. Experts from DecarbCH can support industrial companies in carrying out feasibility studies and all further steps as planning, construction and monitoring of SHIP systems in Switzerlannd.
SOLIND tool
The scientists at the SPF and HEIG-LESBAT have developed a calculation programme, the so-called SOLIND tool, which emerged from the ‘SolInd Swiss’ project. This programme allows companies to quickly assess whether the use of solar process heat in their industrial Processes makes sense. The tool is freely available for download under the following link: SOLIND TOOL (registration needed)
Index
Choice of collector type
Integration strategies
SHIP in Switzerland
SOLIND tool
References